To consider an application for financing, fill out the form and send it to us by e-mail along with the project brief, or contact our experts
Engineering is a creative innovation process.
Designing a chemical plant, especially a new technological process, from the idea stage to its practical implementation, is a complex task that requires multi-stage solutions.
A comprehensive approach based on the practical experience of the engineering team makes it possible to implement each project efficiently and ensure the achievement of investors' goals in the shortest possible time.
To ensure the success of a project, it is important that all teams of engineers who work on various aspects of the project work closely together to form a single team.
For this reason, the design and construction of chemical plants is usually carried out on a turnkey basis, under the terms of an EPC contract with a single general contractor.
The implementation of a new chemical production project includes the following stages:
• Creation of the project concept.
• Preliminary economic and market assessment.
• Obtaining and analyzing information for making a final decision.
• Detailed economic assessment and definition of key indicators.
• Development of a detailed design of the future plant.
• Management of procurement of materials and equipment.
• Construction and installation of equipment.
• Commissioning and testing.
• Production control.
The need to build large factories today requires from an engineering company a wealth of experience, professional competence and modern design and construction methods.
In the current realities, most clients want to get a ready-made turnkey solution, shifting to the general contractor all the risks and problems that may arise during the implementation of an investment project.
LBFL with its partners is ready to offer you a full range of services related to financing, engineering design, construction and modernization of chemical plants.
We are involved in industrial, energy, infrastructure and environmental projects in many countries around the world, including the EU, USA, Latin America, Africa and the Middle East.
Our professional experience and advanced technologies are the key to the success of the most ambitious investment projects.
Engineering design of chemical plants
The general term "chemical plant engineering" includes all engineering aspects associated with the development of a new chemical plant, modernization or expansion of an existing plant.During the development of each project, an engineering company must evaluate the economic parameters of new technological processes, as well as propose designs for machinery and equipment and think over the optimal layout of the plant.
When designing a new plant, the engineering team must consider numerous customer requirements, existing laws and standards, environmental requirements, and market factors affecting the future plant. Since a chemical plant is usually part of a large chemical company specializing in the production of a particular product, the project must be based on the core interests of the entire company.
When developing design documentation for a chemical plant, the engineering team must take into account the type of product being manufactured, the distance to the sources of raw materials and how they are delivered, the need for fossil fuels and electricity, and much more.
Every production process is born in a laboratory, where basic calculations are made, but the engineering design of a chemical plant goes beyond such calculations due to the need to take into account the real conditions of a large-scale process with its limitations.
The industrial production of chemicals is technologically different from the production of similar products in the laboratory, as the latter usually uses simpler but less efficient methods.
At the dawn of the chemical industry, the activities of a chemical plant differed from that of laboratories only by minor modifications or an increase in the size of the equipment used.
In the 21st century, any new chemical process must go through a number of mandatory steps that will ensure the maximum efficiency of the specified process before it is put into practice. A detailed study in the laboratory of the viability of chemical reactions before use for industrial purposes is an important step, which is aimed at finding optimal conditions and obtaining the maximum product yield.
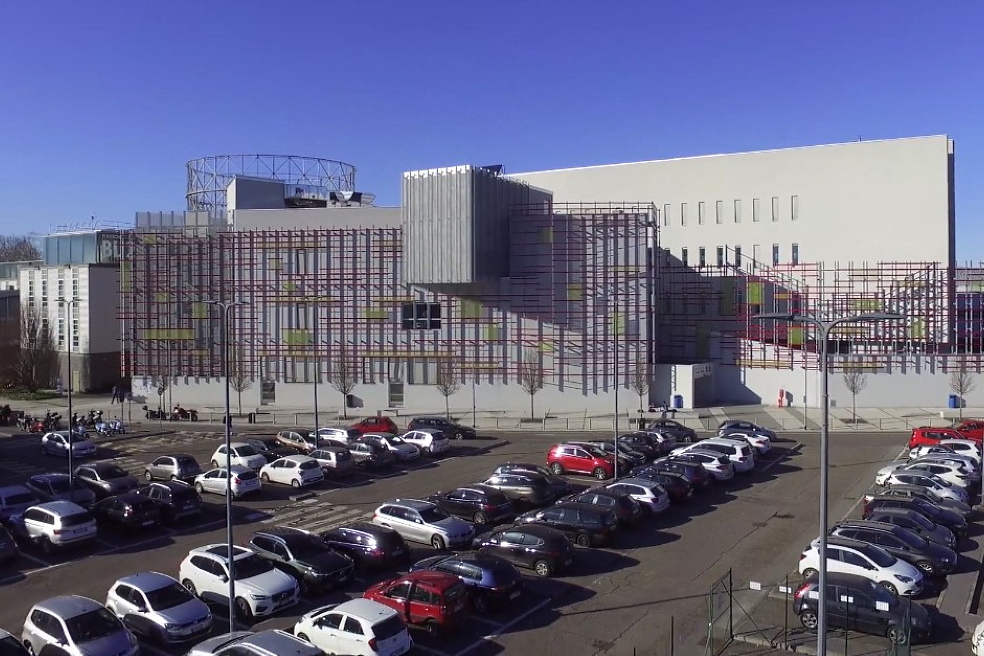
Often, large projects begin with the construction of a so-called pilot plant where the viability of the production process can be tested.
This makes sense as equipment performance and potential risks should be assessed prior to investing in full scale construction. Tests in pilot plants solve numerous practical problems in the production of a specific chemical product.
Classification of chemical plants
Currently, chemical plants are classified according to the type of product and its subsequent use:Production type | Detailed description of production |
Basic chemical industries | The basic chemical industry works with natural raw materials to produce simple semi-finished products. For example, they convert coal, oil, natural gas, phosphates or cellulose into a wide range of products such as ammonia, acids, resins, fuels, fertilizers, explosives, solvents, plastics, etc. These types of factories are usually built in locations close to sources of supply. They require large investments and well-developed infrastructure. |
Production of intermediate chemical products | Intermediate chemical products are stable compounds, each of which can be used to produce several end products, but cannot be used directly by the consumer. As an example, we can mention vinyl chloride, from which various plastics can be produced. |
Fine chemicals production |
These factories produce high purity chemical products with strict quality requirements. These substances are used in the production of pharmaceuticals, reagents, food additives, etc. |
Manufacturing of finished chemical products | The finished substances produced in these factories are supplied packaged, labeled, with the necessary additives and the appropriate concentration of substances for their end use. |
Chemical plants can also be classified by volume of production and degree of product differentiation (large-scale or small-scale, undifferentiated or specific products).
Four major sectors of the chemical industry can be distinguished:
• Mining and metallurgy. Subsectors are distinguished according to the metal or mineral that the factories deal with. The most important are the steel, aluminum and copper sectors.
• Inorganic chemistry. It includes the production of acids, bases, oxides, noble gases, fluorine, chlorine, bromine, iodine, sulfur, nitrogen, phosphorus and silicon compounds.
• Organic chemistry. These chemical plants cover all of the chemistry of carbon and its derivatives. Subsectors include pharmaceutical and cosmetics industries.
• Industrial agrochemistry. Enterprises of this type specialize in the production of chemical products for agriculture. The sector's products ensure the efficient use of plant resources.
In addition to these existing areas, new industries are constantly emerging related to the production of new materials, environmental chemistry, etc.
Chemical plant engineering design stages
All engineering projects in the field of chemical engineering can be divided into three types depending on their purpose and the degree of use of innovations.First, these are projects for the modernization and expansion of existing chemical plants, which usually do not require large-scale changes in already known processes.
Secondly, it is the expansion of production capacities in response to the growth of market demand, which usually represents a copy of proven technological processes with some changes.
Finally, it can be the construction of fundamentally new chemical plants that produce previously unknown chemical products and require the translation of numerous innovative technologies.
Obviously, in the latter case, customers place high demands on the experience and qualifications of the engineering team, since many machines and equipment are developed from scratch based on research data.
Highly qualified personnel and innovative technologies make it possible to implement projects in the chemical industry, regardless of their scale and technical complexity.
Any design work required to develop a new chemical manufacturing process can be divided into two main phases:
• The first phase includes the development of the manufacturing process, covering the steps from the initial selection of the process to drawing up the technological scheme, including the specification of equipment. This work should be done primarily by chemical engineers.
• The second phase includes detailed design of mechanical equipment, design of structures and electrical systems, design of auxiliary units. Engineering companies have dedicated teams with experts from a variety of engineering disciplines. At this stage, cost estimates are carried out, as well as the purchase of equipment and materials.
The engineering design of a chemical plant must begin with clear specifications for product, raw materials and processes. If the project is based on an already known process and products, the costs will be significantly lower. For a new chemical product, a specification will be developed through an economic assessment of possible processes based on laboratory research, pilot plant testing and detailed product market research.
General stages of chemical engineering design include:
• Creation of a general concept.
• Development of a technological scheme.
• Design and selection of equipment.
• Conducting environmental research.
• Measures for plant optimization.
• Organization of operation.
Chemical production flow chart
In the process of engineering design, the creation of a production flow chart simplifies the solution of key problems, indicates the sequence of operations throughout the entire process to facilitate visualization of production processes and indicate the transfer of mass and energy at each stage.There are qualitative and quantitative flow charts that show the information needed in a given process. Block diagrams should contain standard symbols that represent equipment, process lines and the conditions in which they are operated (for example, temperature and pressure).
This stage also involves the development of general requirements for equipment that will be used in a specific chemical production.
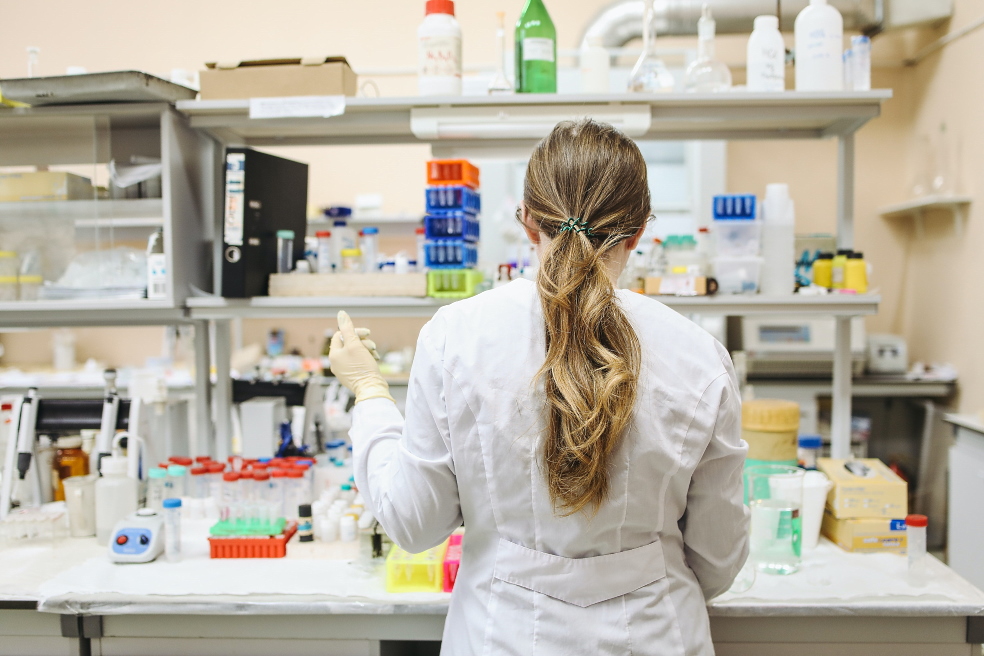
Economic calculations
An important issue in the search for financing for the construction of a chemical plant is the payback period of the investment project.To answer this question, it is necessary to perform economic calculations. The costs of the process must be combined with the costs of raw materials, labor, equipment and other costs, providing an accurate economic estimate of each operation.
Time value of money (TVM), inflation, taxes, and other factors affect profits. These aspects should be taken into account when conducting economic calculations.
Optimization of production processes
Optimization in engineering is a technical term that implies finding the best method to complete a process, that is, reaching the optimum point.It is necessary to select the best way to carry out any process or operation from the existing alternatives.
The engineering team is responsible for this task, which requires the use of mathematical methods and innovative equipment to enable optimal results to be incorporated into the final project.
Optimization of production processes should include two aspects:
• Economic optimization. It includes the design of the technological process, operation and equipment in such a way that the total cost is minimal. If multiple options are available, variable operating costs and fixed capital costs are estimated.
• Technological optimization. The vast majority of chemical processes require specific conditions to optimize their results (temperature, pH or pressure). In many cases, it is possible to partially change these conditions for economic reasons.
Thus, the engineering team needs to take a number of important steps towards developing an optimal design in terms of investment costs.
Chemical plant layout design
Layout is the physical organization of industrial elements in such a way that they constitute a single system capable of achieving their goals in the most appropriate and efficient way.This arrangement includes the spaces required to move materials, finished products, and workers. The goal of any layout is to make manufacturing processes economical and safe.
Construction of a pilot chemical plant
When introducing new chemical industries, pilot experimental plants are widely used today, which reproduce reactions in a very similar way on a small scale to simulate an industrial process.We offer the following services to customers:
• Development of a pilot plant flow chart.
• Sizing and design of the complete set of equipment used in the pilot plant.
• Development of control and automation systems.
• Design, procurement and supply of auxiliary equipment.
• Detailed engineering design.
These services are especially useful when scaling lab-designed processes.
During the operation of the pilot plant, the engineering team can find ways to optimize future large-scale production and identify potential risks associated with new technological processes.
Purchase and supply of equipment for chemical plants
Equipment cost is an important factor in making an investment decision. A preliminary design is necessary in each case to plan the investment costs.For the pre-project estimate, the equipment is indicated without special details.
After the engineering team has made a positive decision, the documentation of the project (detailed engineering) is carried out. This process involves accurate calculations of components, indicating the types of building materials, insulation materials, pipe wall thickness, etc.
The technical documentation developed during the detailed design stage should ensure the procurement of suitable equipment and its smooth installation.
Developing a chemical chain in the laboratory is a first step that cannot be simply transferred to large scale production.
The engineering team will have to address important technical issues to expand production, including:
• Selection of the appropriate type of reactor.
• Search for optimal reaction conditions, including the choice of catalyst.
• Development and optimization of appropriate separation processes.
• Ensuring the supply of fuel, raw materials and energy.
The focus has always been on the cost-effectiveness of the production process, since the engineering design, construction and operation of a chemical plant is time-consuming and costly.
In the planning context, safety and environmental aspects as well as the legal framework, including compliance with official requirements and legal regulations, must be taken into account.
Three main stages of chemical production
The production of any chemical product usually takes place in three stages.Preparatory stage
This phase is used to optimally prepare the starting materials for the actual reaction.For this, the starting material can be crushed, dissolved or heated. Equipment for the preparatory phase is designed and purchased based on the requirements of the second phase of the chemical production.
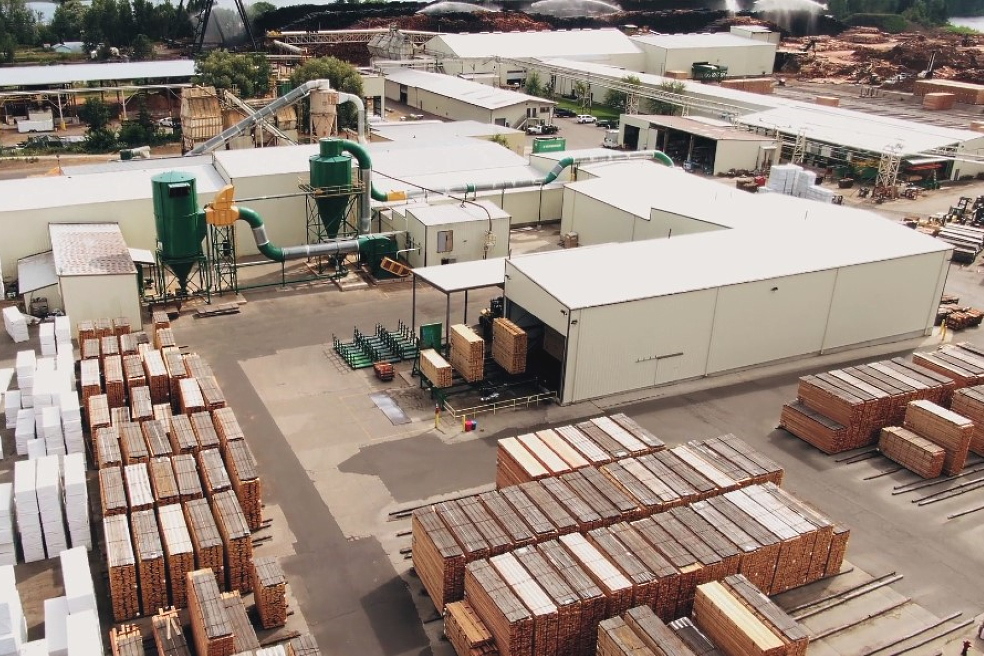
Chemical reaction phase
Any chemical reactions are carried out in reactors of special design, which operate as a cyclic or continuous technological process.Selecting a suitable process and optimal reactor design requires a deep understanding of the numerous parameters of a specific chemical reaction, on the basis of which the material and heat balance is calculated.
Material balance shows the change in the amount of materials in a reactor over time.
For this, the stoichiometry and kinetics under the selected reaction conditions must be known.
Engineering calculations show the maximum capacity for a suitably sized reactor and the daily production of the required chemical.
The heat balance indicates the change in heat over time in the considered volume of the reactor. This parameter is especially important for the supply or removal of energy during the reaction.
The course of any chemical reaction is influenced by factors such as pressure, temperature and concentration of reagents, as well as catalysts. The latter are now used in almost all chemical processes to make them faster and more efficient.
Separation and purification phase
In the last stage of chemical production, the resulting products are separated from the starting materials and by-products.Recovered valuable reagents are usually returned to the reactor and re-involved in the manufacturing process.
The separation and purification phase is one of the most important, since it accounts for the largest operating and investment costs, which can account for 80% of the total costs for a particular production process.
Equipment for rectification (distillation) deserves the most attention in the engineering design of a chemical plant. This process of thermal separation of substances is energy intensive and therefore expensive. Other separation equipment that is also used in the chemical industry includes different types of filtration systems and centrifuges.
Experienced specialists in the field of chemical engineering are responsible for the selection and procurement of equipment for a chemical plant, as well as provide advice to customers at all stages of design, construction and operation of the plant.
Selection of auxiliary equipment
A complex infrastructure is created around any chemical production, ensuring efficient and uninterrupted flow of all technological processes.At the stage of preparation of reagents and the subsequent stage, a variety of equipment is required for mixing or drying, extraction or condensation of products and intermediates.
Separate chemical compounds must be supplied and removed, which requires special pumps and piping systems.
It is important to store liquid chemicals and solvents safely in specially equipped containers. Waste and wastewater from a chemical plant must be disposed of separately, for which special treatment facilities are being built on the territory of the plant. It is important to clean the exhaust air from chemical production using filtration systems.
Currently, the main priority in the design of chemical production is safety and minimization of risks to personnel and the environment.
In the chemical industry, the highest safety standards are applied, so the plant must be constantly monitored by automated systems. Temperature sensors in reactors and flow meters in pipes and chemical hoses measure inflow or outflow in real time, signaling any deviations to operators.
Safety valves ensure the prevention of toxic leakage in an emergency.
All materials of gaskets for reactors and piping systems and chemical hoses for transporting aggressive media must necessarily correspond to the type of chemicals used, temperature and pressure.
Thus, a properly designed chemical plant is a highly complex engineering system in which all components work safely and reliably and must be matched to each other.
Currently, there is a trend towards miniaturization of factories, which, combined with the growth of automation and the emergence of Industry 4.0, leads to significant changes in the design and construction of chemical plants.
Environmentally friendly raw materials are increasingly used in the production of chemicals, and innovative biotechnological processes are gaining in importance.
SWIG and its partners are continuously working to improve the efficiency, safety and profitability of chemical production.
New developments from European laboratories are becoming available to our customers to offer higher energy and material efficiency in every process.